
The iStream production method brought with it the fundamental qualities of which it purports to offer. The MOTIV.e was born and proved the production process beyond the original T.25 and T.27 prototypes. Their aim was to put the iStream process to the test and create a small car that Yamaha could offer as a fun, safe and reliable commuter car.
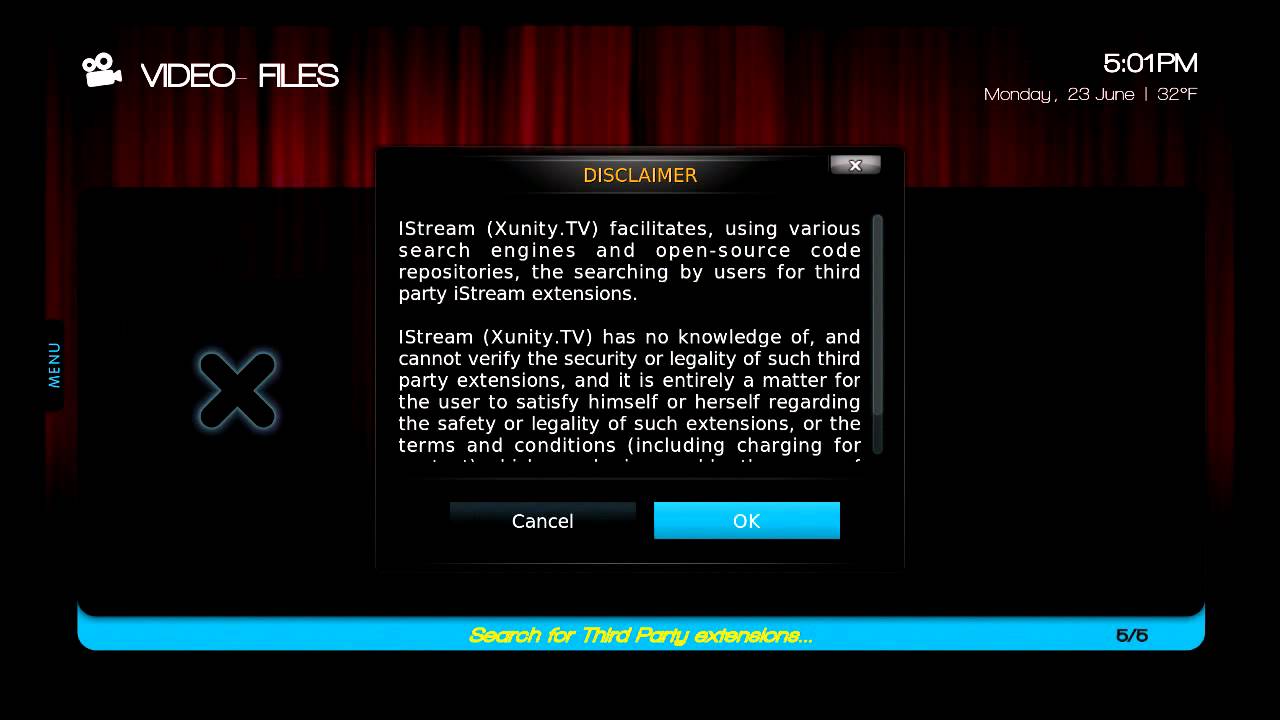
Speaking at the press launch Murray said, “Designing green cars is every bit as demanding as engineering Formula One cars and many of the same principles apply – the search to save weight and maximise efficiency.”Īfter T.27, GDM teamed with Yamaha – a brand not usually associated with cars at all. This showed the world one of the many important benefits associated with iStream production methods crash safety. Importantly for a small car and likely using knowledge gained from years at Formula One, the T.27 scored remarkably well in crash tests, completing the mandatory EEC 40% offset deformable barrier front high-speed impact test, the T.27 emerged with zero cabin intrusion. The following year, Murray unveiled the T.27, which was a derivation of the T.25, but this time featuring electric power.
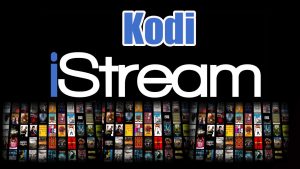
As well as these, the iStream manufacturing process was awarded the SMMT’s Automotive Innovation Award. Lauded as an instant success by the press, the car went on to win, ‘Most Economic Small Passenger ICE Vehicle’ and ‘Most Economic Environment Friendly Small Passenger ICE Vehicle’ awards. In 2010, the company was ready to show their product to the press and at the inaugural RAC Future Car Challenge, they displayed their shiny new car. Crucially, it was designed and built using a new in-house manufacturing process called iStream. What they were creating was called simply the T.25 – a small commuter car with quirky doors and a McLaren F1 style central driving position. Most of his McLaren design team followed him there and together they set to work on designing a rather different machine to the heady performance vehicles they created for Formula One and McLaren. In 2007, Murray decided to branch out alone and formed his own consultancy Gordon Murray Design (GDM). While still at McLaren, Murray toyed with the idea of composite materials for chassis use and the application of it for industry. While at the latter, Murray somehow found time to design road cars and the legendary McLaren F1 was born – featuring BMW power and an almost unmatched performance even today – particularly as it could seat three persons whereas most cars of its ilk only manage to accommodate two. He worked in Formula One for almost 40 years, first at Brabham and then at McLaren.
#Install istream driver#
He earnt legendary status in Formula One, not as a driver but as a designer and Technical Director. Gordon Murray, for most people, needs little introduction.

The iStream process aims to end that system altogether, using instead composite materials to form the chassis and panels of a car, rather than rely on sheet metal, as per convention. These panels often require further processing, for example welding and painting to achieve the end result – a metal car construction.
#Install istream install#
These may save money in the long run, but are initially very expensive to install and setup.įor decades, cars have been made with sheet metal which is shaped into panels by huge stamping machines. Tooling accounts for a large proportion of the cost, particularly as a huge chunk is now done by automated robots.

Traditional manufacture has always consisted of enormous investment for a factory and huge amounts of costly tooling. Little has changed since the days when Henry Ford first introduced the concept of manufacturing vehicles on a mass scale, with his Ford Model T. Using methods and techniques from the likes of Formula One its creator, Gordon Murray, believes his new system is able to provide the same high quality output as you would expect from a traditional production line, but at a fraction of the cost – both environmentally and in price. We investigate how it works. iStream is a radical new vehicle manufacturing process which aims to change the way car production is done forever. iStream aims to do just that for the small-medium volume car industry. Rarely is a production process able to radicalise a method used for decades.
